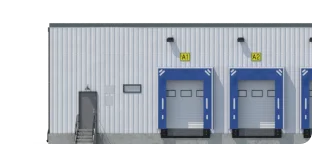
Rental of warehousing and storage facilities

























Warehouse rental is a logistics service that involves providing the customer with temporary access to premises for the storage of goods and materials.
Warehouse rental for storage is formalized through a specialized contract, the form and terms of which are regulated by legal standards. The contract solely covers the temporary use of the premises, while matters related to staffing, equipment installation, and internal process management must be addressed separately.
Today, the service of renting warehouse space is in demand among businesses for solving the following tasks:
- Expanding geographic presence without the need to purchase or equip additional warehouses.
- Optimizing business processes and gaining a competitive advantage through faster delivery of goods to regions.
- Saving resources by avoiding long-term investments in infrastructure.
Warehouse rental differs from responsible storage. In the former, the owner provides the property for temporary use, whereas in the latter, the client receives comprehensive services. Responsible storage is a qualified type of service that includes sorting, preparing, and overseeing cargo during transit.
Modern warehouse facilities vary in capacity, layout, equipment, and additional services. To ensure that the warehouse rental service meets the goals and needs of the tenant, it is important to correctly determine the type of warehouse required.
By Purpose
- Public warehouses belong to entities whose business involves providing comprehensive storage and distribution services. Typically, these warehouses are used for short-term storage, with fees charged per shipment. Examples include marketplaces' fulfillment centers.
- Production warehouses are owned by a legal entity and used for storing products it manufactures or sells. Goods may remain here for extended periods, where they are packaged and distributed.
- Transit-logistics centers are designed to receive goods from manufacturers or suppliers, sort them, and distribute them to retailers, final recipients, or other customers.
- Customs warehouses are used for accumulating and distributing goods imported from abroad.
- Reserve warehouses are utilized for stockpiling essential items in case of emergencies.
- Trading warehouses are intended for temporary storage before goods are distributed to retail outlets for sale.
- Self-storage facilities are rented by business owners to secure various types of goods, including seasonal inventory.
By Storage Conditions
- Specialized storage facilities allow for the placement of goods requiring specific environmental conditions. These include climate-controlled warehouses that maintain optimal temperature and humidity levels for pharmaceuticals, electronics, food products, and similar goods. A separate category includes refrigerated and freezer storage units.
- Dry warehouses do not have the technical capability to create special conditions or regulate temperature and humidity.
- Manual storage warehouses lack automated equipment, and all handling operations are performed manually.
Warehouse Classification by Class
The most convenient method for evaluating all warehouse parameters is their classification by class. According to this system, there are six types of warehouses:
- A+ — modern single-story facilities equipped with necessary utilities and meeting safety requirements, typically constructed from sandwich panels with optimal ceiling heights and 24/7 security.
- A — slightly inferior to A+ warehouses only in terms of ceiling height (up to 10 meters) and ease of loading/unloading operations.
- B+ — newly built or renovated facilities with maximum ceiling heights up to 8 meters.
- B — multi-story warehouses with minimal technical requirements, except for mandatory freight elevators; maximum ceiling height is 6 meters.
- C — converted from former production facilities, with ceiling heights up to 4 meters.
- D — the lowest-class warehouses, considered non-specialized and subject to no technical requirements.
This diversity of storage options allows businesses to choose the one that fully aligns with their operational needs.
Renting a warehouse or production space is essential for the rational allocation of resources and efficient use of available areas. It makes sense when:
- The business owner plans to expand, requiring the relocation of assets to alternative storage, and rental costs are lower than the anticipated expenses for responsible storage services or purchasing storage facilities.
- There is a need to store large quantities of goods that do not require special conditions or the use of warehouse equipment.
- Simple logistics schemes suffice, meaning there are no immediate plans to change shipment volumes, types of cargo, or geographic presence.
- The company has its own staff capable of managing the warehouse and performing all necessary tasks while ensuring compliance with the owner's requirements, maintaining confidentiality, and adhering to commercial secrecy.
Renting space for a warehouse or production facility is cost-effective for small shipment volumes. A significant advantage of this logistics solution is the payment structure, as rent is charged solely based on the area used, regardless of the number of units or their volume. The key is ensuring that the storage conditions meet safety requirements for the goods being stored.
Renting a warehouse is a complex, multi-stage process that requires meticulous analysis and consideration of all aspects. To rent a warehouse efficiently, avoid unexpected situations or unjustified expenses during use, and optimize logistics, it is advisable to follow seven sequential steps.
1. Situation Analysis and Defining Needs: Area, Location, and Lease Duration
First, it’s important to assess the required size of the warehouse.
Paying for unused space is inefficient, while an overly cramped facility can complicate inventory management, cause sorting issues, and even lead to violations of storage rules, potentially resulting in damage to goods. It’s prudent to consider business growth prospects so that expanding production or shipment volumes doesn’t necessitate searching for a larger space immediately.
The rented space should be strategically located near logistics routes, suppliers, and recipients, as well as ensure security.
2. Cost Planning
Before signing a lease agreement, it's essential to review various offers and select the most suitable one.
The rental cost depends on the warehouse location, type, amenities such as heating, electricity, and water supply, as well as additional expenses like taxes, repairs, or modernization.
3. Selection of the Optimal Option
There are many ways to find a suitable property for rent. You can search independently by reviewing online listings and social media, or you can engage professional commercial real estate brokers. The latter option is often more promising.
Brokers have access to extensive information, can warn against potential pitfalls, and handle negotiations on your behalf.
4. Direct Evaluation of the Storage Facility
Visiting the premises before signing a contract is mandatory. This allows you to assess its condition and suitability, inspect structures and utilities for wear and tear, and determine how well it meets your needs, including transportation accessibility.
5. Signing the Lease Agreement
Key terms of the lease agreement are regulated by the civil code, and their absence renders the document invalid. Therefore, it is crucial to carefully review and sign the lease agreement after consulting with a legal expert.
6. Preparatory Measures
After signing the documents, the tenant typically pays a security deposit and advance payment. All financial transactions should be meticulously recorded and documented.
This stage involves preparing the warehouse for cargo placement, conducting necessary repairs, installing and configuring equipment, planning logistics, and determining the required workforce and qualifications.
7. Using the Warehouse
Once the goods are moved to the new warehouse, employee training, implementation of inventory management systems, and safety measures must be carried out.
Ongoing maintenance and periodic repairs are generally the responsibility of the tenant unless otherwise specified in the contract.
Following these stages ensures a structured approach to renting a warehouse, minimizing risks and optimizing resource allocation for long-term efficiency.
Warehouse rental offers several advantages over other storage organization options, including:
1. Provides greater assurance of asset security
Warehouse premises are reliably protected from unauthorized access, often featuring alarm systems or 24/7 security guards, ensuring the safety of stored goods.
2. Helps save on budget
Business owners who opt for renting do not need to construct their own warehouses, pay for unnecessary additional services, or allocate production space for storage purposes. This reduces initial investment and ongoing operational costs.
3. Simplifies operations
Properly organized storage allows for efficient inventory management and timely deliveries, streamlining logistics processes.
4. Expands business capabilities
Having a rented storage facility makes it easier for companies to organize their work. It provides flexibility in choosing storage methods and optimizing access to goods. However, these advantages can be negated if the rental price is excessively high, the space cannot be used efficiently, or the warehouse location is too far from key transport hubs.
When chosen wisely, warehouse rental enhances logistics efficiency while minimizing risks and costs associated with storage.
The cost of renting a warehouse is determined on an individual basis in all cases, and numerous factors influence this aspect, including:
- storage duration
- type of warehouse and availability of equipment for maintaining special storage conditions
- characteristics of the goods, their volume, and specific requirements
- specifics of loading and unloading operations and the complexity of the process
- availability of additional services
The rental cost is calculated for the entire area, regardless of the amount of property planned for storage or the chosen operational scheme.
To avoid making a wrong choice when selecting a landlord, consider the following criteria:
1. Warehouse Location
It’s important to evaluate the accessibility of the transport infrastructure and the condition of access roads. If certain seasons make the warehouse inaccessible due to flooding or unusable roads, the feasibility of renting it comes into question, no matter how attractive the price might be. A significant advantage is the availability of office space for rent near the warehouse.
2. Property Parameters and Characteristics
The storage facility should be assessed in terms of its area, capacity, and technical condition. To use the rented property effectively, it must meet your needs without creating additional challenges like the need for major repairs, installation of utilities, or approval of renovations.
3. Availability of Necessary Equipment
Automation of warehouse processes and the presence of specialized equipment significantly simplify operations and contribute to the safety of goods. An electronic database ensures accurate accounting and control.
4. Level of Security
Warehouses vary in their security class. Choose a facility based on the required level of protection for your goods.
5. Logistics Services
If needed, check whether the landlord offers additional services such as product packaging, organization of transportation, inventory management, and handling of defective items.
Of course, pricing is an important criterion for any tenant. Initially, companies tend to focus on the most cost-effective options.
However, remember that low rates often correlate with lower service quality. The mid-price segment typically offers the best balance between cost and reliability.
A logistics company offering warehouse rentals can be easily found in the Roolz directory. Choose a reliable partner or add your company to explore new logistics opportunities through the Roolz platform!
What is warehouse and storage rental
Warehouse rental is a logistics service that involves providing the customer with temporary access to premises for the storage of goods and materials.
Warehouse rental for storage is formalized through a specialized contract, the form and terms of which are regulated by legal standards. The contract solely covers the temporary use of the premises, while matters related to staffing, equipment installation, and internal process management must be addressed separately.
Today, the service of renting warehouse space is in demand among businesses for solving the following tasks:
- Expanding geographic presence without the need to purchase or equip additional warehouses.
- Optimizing business processes and gaining a competitive advantage through faster delivery of goods to regions.
- Saving resources by avoiding long-term investments in infrastructure.
Warehouse rental differs from responsible storage. In the former, the owner provides the property for temporary use, whereas in the latter, the client receives comprehensive services. Responsible storage is a qualified type of service that includes sorting, preparing, and overseeing cargo during transit.